Jahvataja OÜ, an innovative agriculture company in Estonia, was held back by outdated processes. To break free from manual struggles, they teamed up with Waybiller and adopted a digital grain terminal solution. They set the stage for a transformation that simplified workflows and improved accuracy—a shift that paved the way for a new era in their operations. Read on to uncover the details.
About the company Jahvataja OÜ
- Industry: Agriculture
- Employees: 25
- Location: Estonia
Before and after Waybiller
Before adopting Waybiller, Jahvataja faced common problems in agriculture logistics and grain terminal management:
- Disconnected Systems – paper waybill storing, slow data entry, and lots of manual data entry throughout the process, that made workflow slow, inefficient, and prone to errors.
- Manual Processes – scale house workers were responsible for recording weighing and laboratory data, assigning stocks, keeping track of inventory, filling in the grand book of information etc. Such repetitive manual data entry was time-consuming and was prone to mistakes
- Human Error – manual and disconnected processes caused errors in entering data and delayed reporting.
Jahvataja partnered with Waybiller to digitise its logistics and improve operations. This transformed their processes and efficiency:
Before | After | |
E-waybills | All paper waybills had to be filled, handled and stored manually. | E-waybills replaced paper processes with a digital system, providing real-time access to transport data, reducing paperwork, and improving operations for the entire team. |
Scale integration | Weight data had to be recorded manually, often leading to mistakes. | Integrating scales automated weight data collection, sped up weighing, eliminated errors, and provided access to accurate real-time weight information. |
Stock management | Stock levels were entered and tracked manually, which led to discrepancies. | E-waybills enabled automatic stock entries. This resulted in improved accuracy and real-time access to information. |
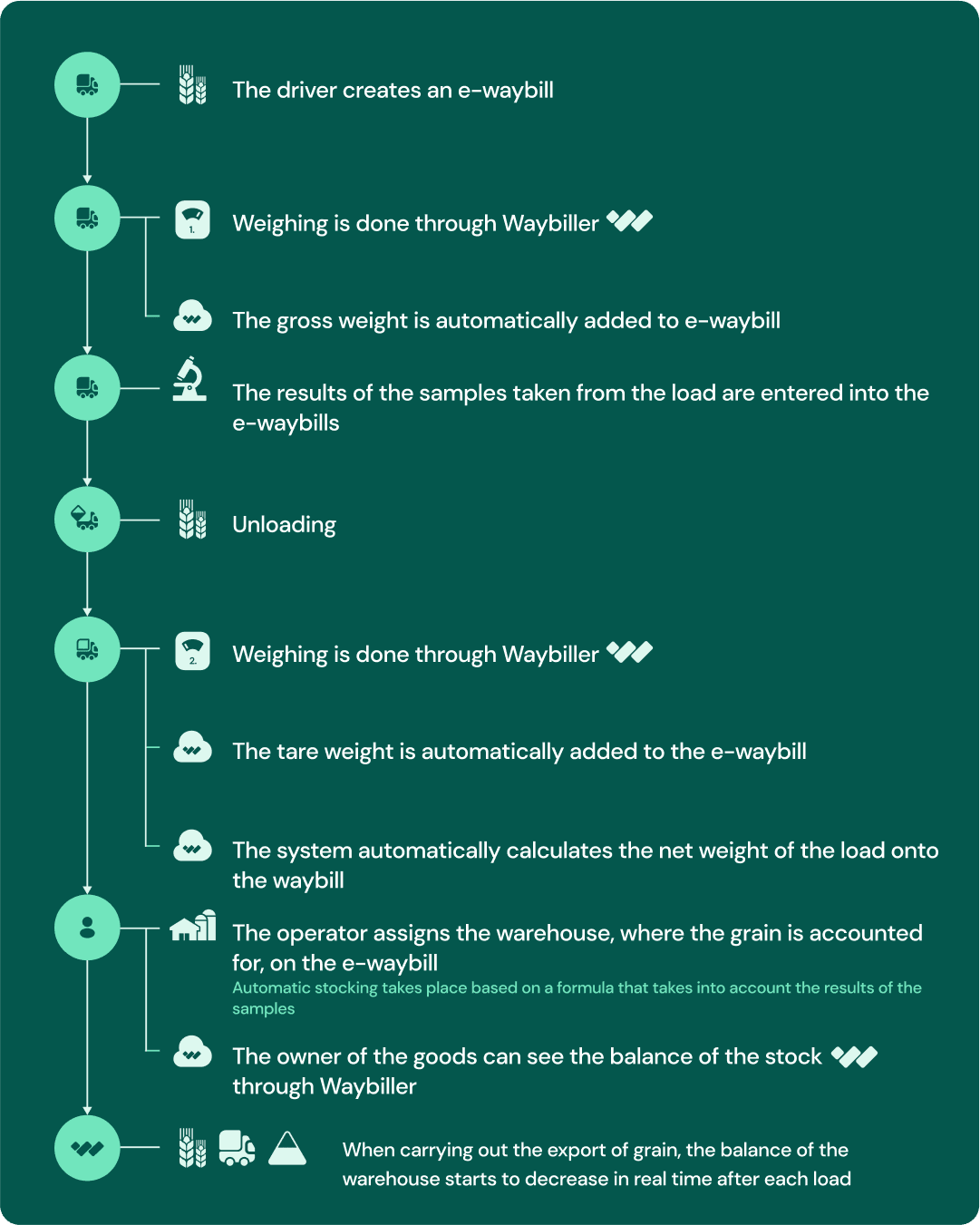
Tech stack & processes
Before: Jahvataja relied on paper waybills and manual data entry, with scales and laboratory systems operating separately. These disconnected tools created bottlenecks, leading to frequent errors, delays, and inefficient logistics and reporting.
After: Waybiller provided a unified digital grain terminal solution, replacing manual processes with an e-waybill platform. Digital e-waybills, automated scale integration, and real-time stock tracking centralised all logistics data, making it accessible to everyone involved.
Introducing e-waybills
Before: paper waybills had to be collected, and filed, and the data was later entered into spreadsheets. Reporting was slow, and it was hard to keep track of records.
After: Waybiller introduced digital e-waybills, which significantly simplified logistics. Drivers use smart devices to create transport documents, while lab and scale house workers can see truck arrival in real time and get acquainted with documentation, making operations effortless and precise.
Key benefits:
- All logistics documents are stored online in a single system.
- Everyone has access to real-time and historical transport data.
- It’s easier to analyze field-based crop yields.
“Waybiller’s e-waybills have cut down our paperwork and made our operations more efficient,” says Allar Neeme, Jahvataja’s Manager.
Integrating scales
Before: weight data was written down by hand, often leading to mistakes. This slowed down the truck loading and unloading process.
After: Waybiller integrated the scales into its system. Drivers now trigger weighting on the scale dependent on location technology either using QR codes, license plate recognition, or app buttons. The weight data goes straight onto the e-waybill, eliminating mistakes.
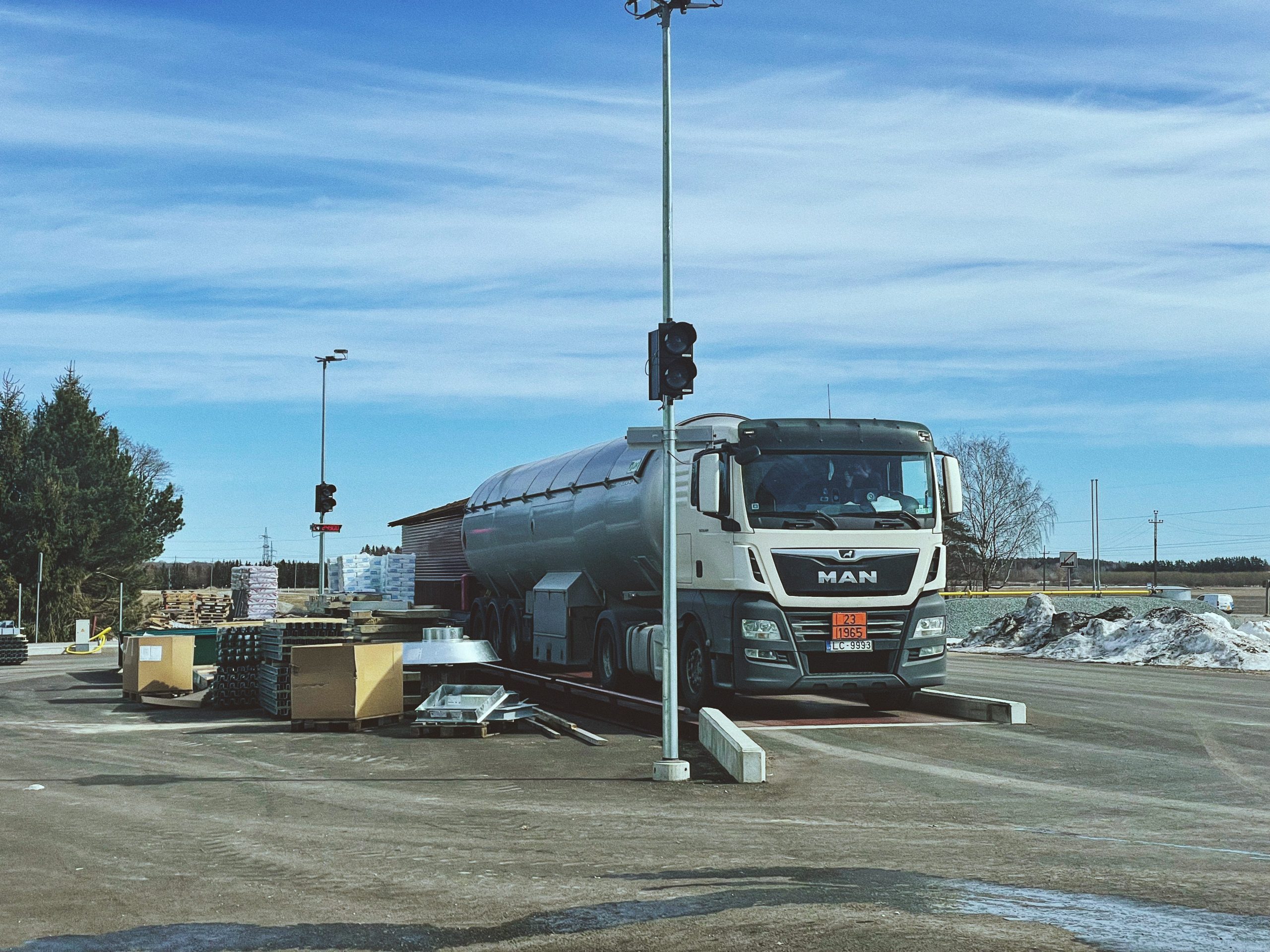
Key benefits:
- Weight data is entered automatically, reducing human error.
- Trucks are loaded and unloaded faster.
- Weight data is available online in real time.
Digital grain stock management
Before: stock updating was manual and time-consuming, also there was no good real time overview of stock balance. Mistakes and slow information flow made planning and communication difficult.
After: Every load is digitally recorded and stock levels update automatically based on e-waybill data. Data moves in real time and is easily accessible online.
Key benefits:
- Access to real-time stock levels at all times.
- Less repetitive manual work for employees.
- It’s easier to accurately plan logistics and storage capacities.
Implementation and training
Onboarding to the new paperless grain terminal at Jahvataja was fast and effortless. Employees worked closely with Waybiller’s project manager for a smooth and quick setup. It consisted of preliminary data entry, on-site training, and written manuals for various use cases. After the training day, Jahvataja assigned a software specialist as the main point of contact for managing the system on their side.
Steps taken:
- Staff received pre-launch training.
- A dedicated account manager provided ongoing support.
- Training materials were created for new employees.
“We were running smoothly in just a few months, thanks to Waybiller’s simple setup,” notes Allar Neeme.
Ongoing support
Waybiller continues to support Jahvataja with a dedicated team and quick problem-solving. Customer support is easily accessible, and the appointed internal contact ensures that all new employees are properly trained and understand the new process. Waybiller regularly conducts feedback surveys to gather insights and new ideas on how to further improve the solution.
“Waybiller’s support team has been fantastic. They’re always quick to help and regular feedback sessions make all the difference,” says Allar Neeme.
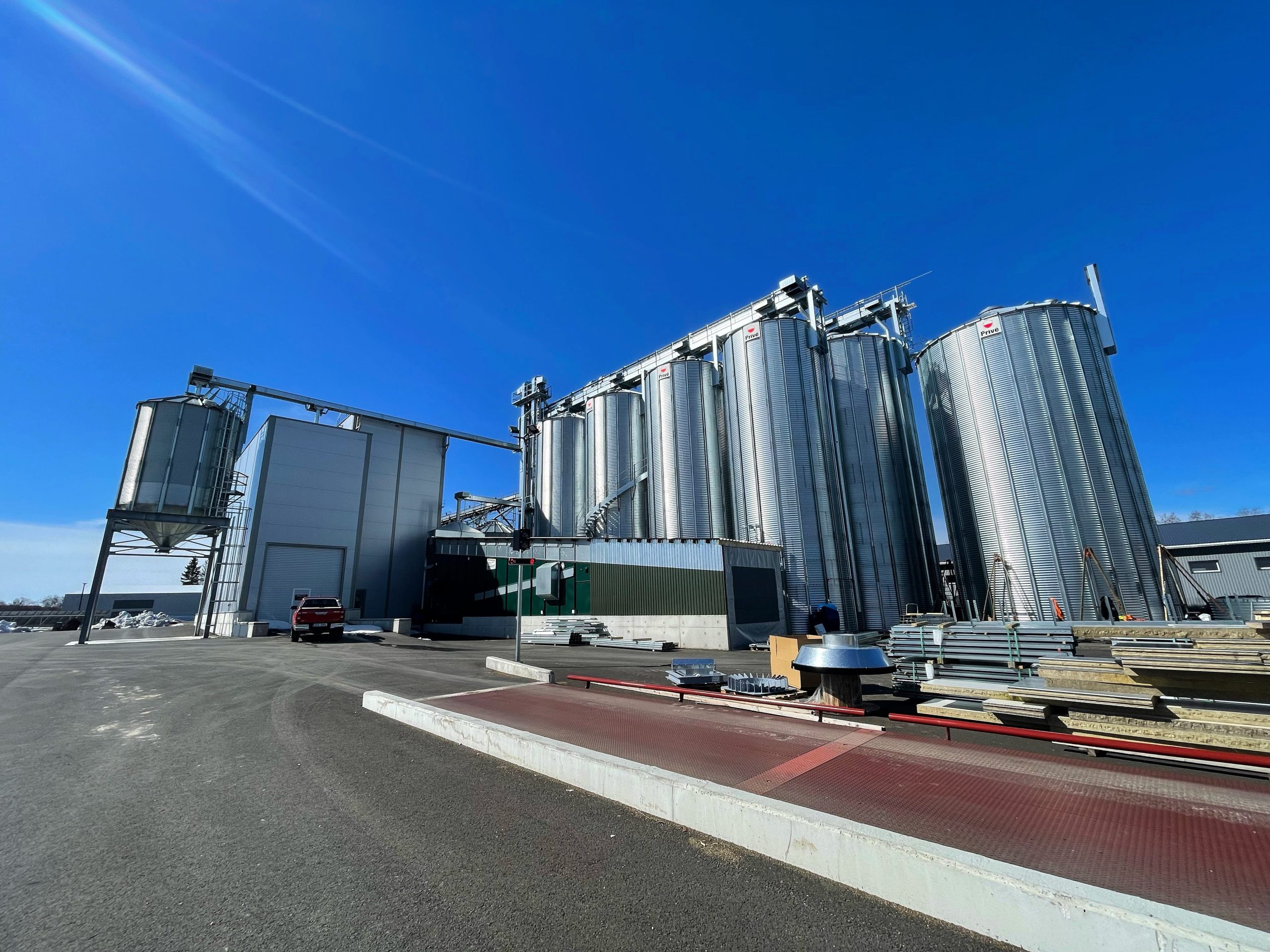
The results
Waybiller’s digital grain terminal solution transformed Jahvataja’s operations. They became a truly paperless company and reduced hours spent on manual data entry. Today, the employees can’t imagine why anyone would still use paper waybills. By switching to digital e-waybills, integrating scales, and implementing online stock management, they have:
- Less manual work.
- More accurate data.
- Real-time insights for smarter decisions.
“The future of agriculture logistics is digital. Waybiller has helped us take a big step forward,” concludes Allar Neeme.
Ready to go paperless? Sign up for a Waybiller demo today!